CLEAN WATER… PURE OIL… NO CHEMICALS…. REDUCED LABOR…. HAUL AWAYS DOWN… COMPLIANCE!
About US

The Fogbusters™ System is a revolutionary technology for removing fat, oil and grease (FOG) from wastewater.
This elegantly simple, patented technology works in conjunction with your current DAF, centrifuge, biological or other treatment systems to recover the FOG from your wastewater with little to no chemicals. The FogBuster™ can be installed (1) at the head of your oily wastewater before it reaches your DAF, (2) in your process rooms where you can capture FOG in its purest form (3) in place of your current DAF or other system. Whatever the situation, the FogBuster will fit into your existing process to minimize downstream load and maximize recoverable oil

- Do your current systems overload with too much FOG?
- Are your chemical and sludge costs high?
- Do you struggle to stay in compliance?
- Do you want to sell your recovered oil as biodiesel feedstock?
pouring out beneath it.
Fogbuster 3800 In Action – Harvests 5-7,000 lbs a day of recovered oil marketable as biodiesel feedstock. Harlan, IA.
Contact FogBusters NOW. We are a known oil-water separation solution that puts you in compliance, saves you money, and generates new revenues.
The PAIN

Dissolved Air Flotation (DAF) is a traditional technology for FOG removal.
DAF requires costly chemicals and produces an oily mixed-waste sludge that must often be disposed of in landfills at significant cost. Moreover, DAF works only in a narrow pH range, is effective only on wastewater with low FOG concentrations a fails at higher oil concentrations a is labor intensive.
- Labor Intensive
- Requires costly chemicals
- Produces a sludge that must be hauled away and disposed of in landfills all at significant cost.
- Works only in a narrow pH range
- Is effective only on wastewater with low FOG concentrations
- Fails at high oil concentrations
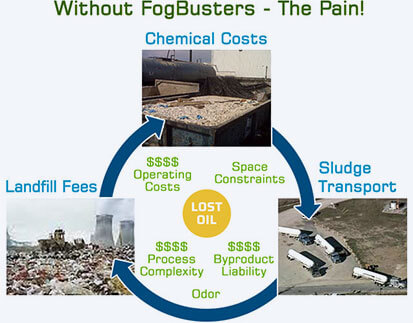
The Gain

Key Features & Benefits
- Extracts FOG without the use of chemicals.
- Extracts and compacts gross solids.
- Keeps you in compliance.
- Reduces carbon footprint.
- Works stand alone or alongside current systems
- Cuts sludge trucking and disposal costs.
- Requires costly chemicals
- Is effective only on wastewater with low FOG concentrations
- Requires costly chemicals
- Is effective only on wastewater with low FOG concentrations
- Requires costly chemicals
- Is effective only on wastewater with low FOG concentrations
Small footprint. Works at any pH. Indoor or outdoor use.
A proven system in routine commercial use in multiple industrial applications.
High effluent throughput (up to 350 GPM per module).
Handles palm oil, coconut oil, animal fats and other “problem oils.”
FOGBUSTER APPLICATIONS

The Fogbuster works on a wide range of applications including the following:
- Vegetable Oils Case Study Click here
- Meat & Poultry Further Processing Case Study Click here
- Rendering Case Study Click here
- Processed Foods Process Rooms Case Study Click here
- MRE's & Frozen Foods Sauces and Dressings Case Study Click here
- Mayonnaise, Butters, Margarines. Chips Chocolate Case Study Click here
- Dairy
- Nut Oils
- Baked Goods
- Petroleum
- Ethanol Production
- Marine (Bilge Water)
- Lotions/Cosmetics
- Pet Foods
- Soaps and Surfactants
- Pharmaceuticals
- Tanneries
- Surfactants
- Transportation (motor oil)
Process Rooms: (frying, roasting, baking, microwaving, steaming)
Case Study Click Here
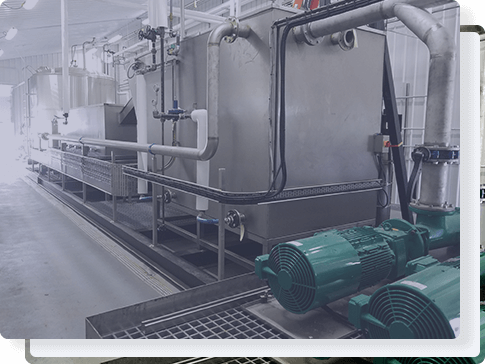
The Technology

Summary:
The FogBuster reliably removes fat, oil and grease (FOG) from industrial wastewater streams with higher efficiency and lower cost than other systems. The Fogbuster can also significantly reduce COD, BOD and TSS. In wastewater with gross solids, the optional Fogbuster L’Vala solids extraction module removes and compacts floating and sinking debris from the effluent. The technology works in a broad range of temperatures and pH and can handle effluent with any oil content – including 100% as in the case of an accidental spill.
Detail:
The FogBusters System is based on patented and patent-pending hydraulic technology. The Fogbuster can have up to three stages depending on wastewater volume and complexity.
Effluent first enters the Fogbuster via its primary stage (Balancing Tank) where, if necessary, the gross solids are first removed using the optional L’Vala compressive . The auger compression dewaters the solids and reduces their volume by up to 90% for economic disposal. In the Balancing Tank the Fogbuster also “balances” the flow of FOG and water into the ideal concentration for the secondary stage, the Separator, which extracts the FOG from the wastewater. If the FOG in the incoming effluent exceeds 50%, a sensor triggers the system to briefly close the effluent inflow valve and open a fresh-water valve to dilute as necessary. Once the mix is diluted to below 50% oil, the system reverts to normal. Other sensors detect excessive effluent levels within the unit, flow rate and outlet effluent quality.
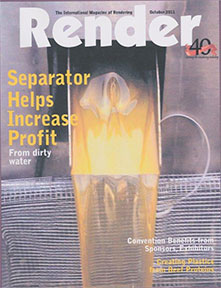
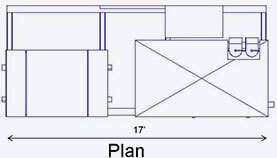
The FogBusters utilizes specific displacement and a series of geometrically precise baffles (floating and fixed) to achieve the balance and extraction required. These baffles track the interface between FOG and effluent thereby creating a “wall” of FOG. All effluent is directed through this “wall” which acts as a filter to further remove FOG. As a result of the FOG removal there are reductions in BOD, COD and TSS in part because a proportion of these contaminants “stick” to the FOG. The Separation Tank then extracts the FOG from the wastewater and ejects it under gentle pressure through a series of valves at the top of the separation chamber. From there, the highly concentrated oil flows via gravity into a reservoir attached to the side of the Separator and then automatically transfers the recovered oil to a holding tank via a sensor-activated pump. The extracted FOG is highly pure with low moisture content.
Where required, a Final Recovery Tank will target any remaining FOG and re-circulate it to the start of the Fogbuster system for further processing.
The entire system is controlled and fully automated by Allen-Bradley or Siemens PLC touch screen controller interface. This interface is compatible with a variety of data communication technologies.
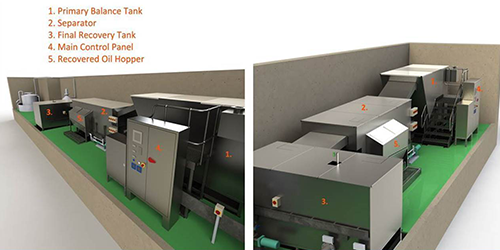
Capabilities
- Up to 99.8% reduction in FOG with moisture content in the extracted oil as low as 0.3%.
- Up to 25,000 gallons per hour effluent throughput (FogBuster Model 2800).
- Indoor or outdoor operation.
- 24/7 operation 365 days/year.
- Skid-mounted for easy transport and forklift movement.
- Modularized for side-by-side installations at larger sites.
- Any pH.
- Automatically senses the presence of incoming effluent with an oil content >50% (as in a spill) and dilutes as required for the separation process.
KEY CHARACTERISTICS
- Gravity-flow system. (There are no water pumps within the unit.)
- No chemicals or polymers (flocculent) required.
- Effluent enters at one end, flows lengthwise and exits from the far end.
- Included oil pump automatically pumps out the oil reservoir into a storage tank.
- Oil/water separation runs entirely on hydraulic force generated by the flow of effluent through the system (via a proprietary system of chambers, baffles and weirs).
- No skimmer mechanisms; no air pumps.
- Purified oil exits the top or side of the separation tank and flows into an integrated reservoir on the side of the tank.
sample PHYSICAL DIMENSIONS – the fogbuster comes in multiple sizes
- Skid-mounted for easy transport and forklift movement.
- 3’ clearance required around all sides.
- The Fogbuster consists of one to three stainless steel tanks in series.
- The Balancing (first) tank is 8’ long, 5’ wide and 8’ high.
- The Separator (second tank) is 5’10” long, 4’6” wide and 4’ high.
- Dimensions: 17’L x 8’W x 10’H. (Height 12’ with optional augurs.)
- Weight including skid: 7,000 lbs.
- Optional twin 5.0 horsepower augurs are mounted on first tank for solid removal.
- The unit also includes:
- A weather-proof Siemens or Allen-Bradley PLC computer control panel measuring 3’6” square.
- A gantry to access the top of the Balancing Tank and the optional augurs.
typical services required
- Hook-up to 3-phase 480V 60 hz electrical power source with 32 amps.
- (FogBuster is pre-wired. Its integral power module converts the 480V three-phase power supplied into appropriate current for the unit’s PLC, sensors, actuators and oil transfer pump.)
- Hook-up to a compressed air line.
- Hook-up to incoming wastewater and to the appropriate line for outgoing wastewater.
- Hook-up to a 2.2–3.2 psi freshwater intake line. (This is to dilute any incoming oil surge.)
- Preferably, hook-up to a hot water supply (185⁰F) or to a steam return line. If not available, an electric heater and pump for the heating coil will be provided. (This is for heating incoming wastewater where necessary.)
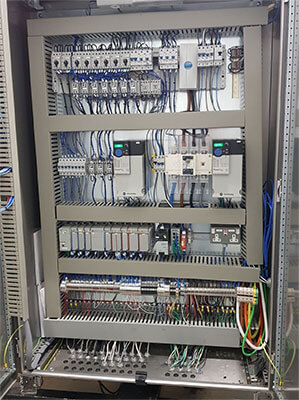
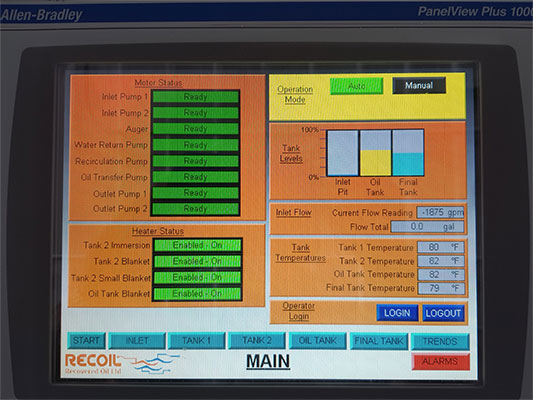
FOGBUSTER RETURN ON INVESTMENT (ROI) ATTRIBUTES
- Increased Oil Recovery: The FogBuster will recover up to 98% of free oil from wastewater or process water.
- Improved Oil Quality: Oil is being recovered at the earliest possible stage, without chemicals, and virtually moisture free increasing the value of the recovered oil.
- Reduced Chemical Usage: When placed ahead of chemical oil elimination systems such as DAF and EAF, the Fogbuster reduces chemical requirements (flocculants, coagulants, diatomaceous earth). Additionally, where the FogBusters solids removal system is used, additional solids removal results in reduced chemical costs.
- Reduced Sludge Disposal Costs: Removal of oil prior to a chemical oil elimination system results in reduced oil levels, which means reduced chemical.
- Minimized Operational Failures: The Fogbuster stabilizes the entire system by eliminating oil slugs and overloads from point of origin through to biological systems.
- Reduced Operational Costs: No moving parts (solids removal in the optional primary tank excepted) results in reduced energy needs and reduced operational and manpower costs. This also includes reduced trucking costs, tipping fees, and municipal surcharges.
- Sustainability: Reduction in landfill of oil/chemical sludge, carbon footprint reduction and corresponding carbon offsets for waste oil are possible. This is “green technology” at its best.
Notes:
- ROI typically less than 12 months
- ROI can be derived from single or multiple benefits depending on the client.
ADDITIONAL FACTORS FOR HIGH PERFORMANCE:
- Continuous flow better than intermittent flow
- Locate FogBuster Oil / Water Separator upstream as close to source as possible
- Oil in water is free oil; not emulsified
- Minimize solids upstream of FB Separator
- Access to steam if wastewater temperature is below 80°F
- “Slugs” of oil / fat are under 50%
- Single, targeted process stream rather than co-mingled streams
- Locate indoors where possible for temperature control
FogBuster Optimal Operational Parameters
Water Data Optimum Range
Water Data | Optimum | Range |
---|---|---|
Flow Rate: | ||
-Model 600 | 25 GPM | 10 to 40 GPM |
-Model 1800 | 100GPM | 50 to 125 GPM |
-Model 2800 | 160 GPM | 125 to 200 GPM |
-Model 3600 | 300 GPM | 200 to 350 GPM |
Oil: | N/A | 0.2% to 50% |
Temperature: | 120°F | 80°F to 170°F |
pH: | 9 | 1 to 131 |
Total Suspended Solids: | Minimal or negligible | 50% or less of oil level |
Download Client Survey Download
sustainability

The ROI and financial impacts from the use of a Fogbuster are significant but it's also about sustainability.
- The Fogbuster gets water cleaner (lower ppm of FOG).
- Reduces landfill usage.
- In some cases, carbon footprint reduction.
- Significantly reduces the use of chemicals.
- Removes suspended solids and insoluble BOD/COD (which are other key contaminants).
- Reduces the generation of oil sludge that otherwise requires trucking costs.
- Reduces the malfunction of downstream wastewater treatment systems.
- Facilitates recycling of waste FOG for biodiesel production and other uses.
Recovers oil in a valuable/saleable form instead of an oily sludge with costly disposal issues.
Most biofuel feedstocks (corn, canola, oil palm and other oil crops) divert cropland and other resources from food production (the food vs. fuel dilemma).
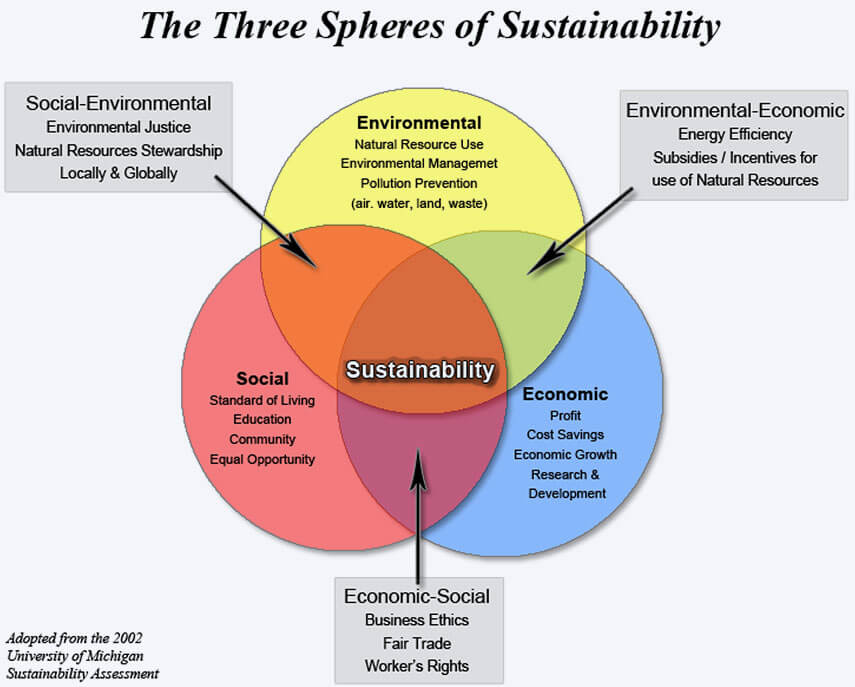
CLIENTS AND CASE STUDIES

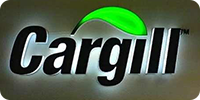
Rendering
Case Study
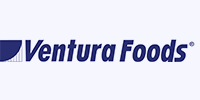
Vegetable Oils
Case Study
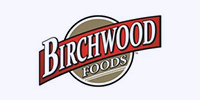
Processed Foods Process Rooms
Case Study
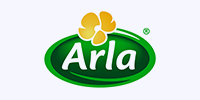
Frozen Foods Sauces and Dressings
Case Study
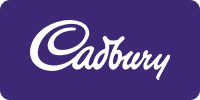
Chocolate
Case Study
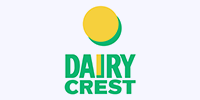
Vegetable Oils
Case Study
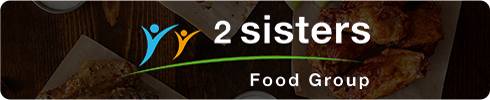
Meat & Poultry Further Processing
Case Study